不断收紧的汽车油耗及排放法规,不仅造就了火热的新能源汽车市场,同样捧热了一批汽车轻量化材料,例如铝合金、镁合金等金属材料以及塑料、纤维增强复合材料等非金属材料。不难发现,随着汽车轻量化的进展,铝合金、镁合金以及高强度钢等材料由于比强度高,使用量增幅明显。而同样不容忽视的是,非金属材料应用比例也在逐渐上涨。相关数据显示,就普通乘用车而言,非金属材料重量占比约1/3,部分车型这一占比更大。
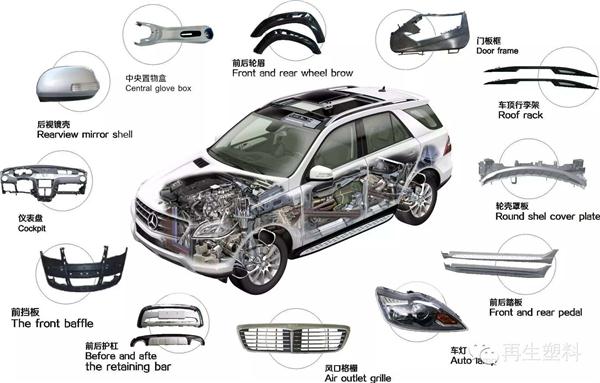
车用非金属材料主要包括塑料、纤维增强复合材料、橡胶、织物皮革、胶粘密封剂等十余种材料。其中塑料、纤维增强复合材料、橡胶、胶粘密封剂常被称为车用非金属四大材料,这些材料在减轻车重、改善舒适性,尤其是成本方面具有相对优势,这也是很多车企倾向于将此类材料应用纳入到近期规划中的重要原因。
近日,在由上海凌傲企业管理咨询有限公司主办的“2017汽车创新材料应用于VOC高峰论坛”中,江淮汽车技术中心材料工程部技术总监黄家奇在其演讲中便指出,目前江淮汽车正在多部门联合开展轻量化金属新材料、新技术、新结构研究,并已制定了相关的实车应用规划。而在非金属材料方面,其目前则已实现多个项目量产应用,例如薄壁化保险杠、复合材料厢式货箱、塑料尾门等等。
其实,大部分车企与江淮汽车的思路基本一致:虽然在金属以及非金属材料方面都有所动作,但现阶段则更倾向于扩大一些非金属材料的使用量。归结原因,无非是在铝、镁合金成本迟迟降不下来,以及还有一些相关的技术问题尚未解决的情况下,以上所提到的几大非金属材料更容易实现规模化应用。
从黄家奇现场所分享的应用案例可以看出,通过对钢板部件的替代,铝合金车架以及铝合金发盖内板等实现了结构设计集成化、生产效率的提高以及重量的减轻,但成本却出现一定的增长,虽然这一增长幅度并不大,但一定程度上会影响到车企在轻量化方案上的决策。
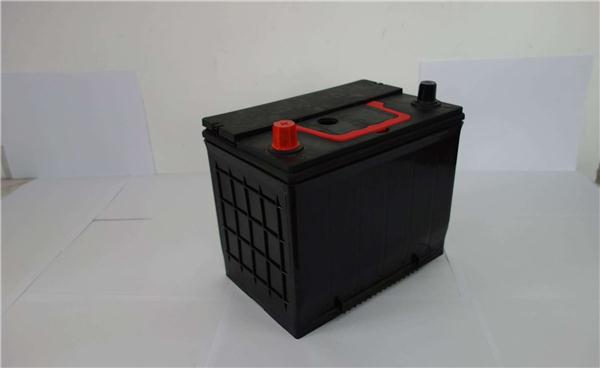
而通过对比可以看出,塑料、纤维增强复合材料等非金属材料不仅具有金属先进材料的优势,在综合成本上也具有一定的优势。举例来说,以LFT(长纤维增强热塑性材料)替代前端模块的钣金不仅可以将重量由原来的7kg降低到6kg以下,成本也可降低约四分之一。除此之外,LFT在塑料电池包壳体上的应用以及RTM在塑料行李箱盖上的应用均实现了成本方面的优化。
上海汽车集团股份有限公司乘用车公司中心实验室高级工程师胡仁其在接受盖世汽车采访时表示,车企通常是根据具体车型的档次以及售价的不同,来决定采取怎样的轻量化方案,因为这关系到它能够接受何种程度的轻量化成本。因此在笔者看来,在仍以中低端车型为主体的中国汽车市场,在车企对于成本仍然较为敏感之时,其所需要的是更具成本优势的轻量化方案。
的确,非金属材料正以前所未有的速度被应用在汽车上。而正如华晨汽车工程研究院项目管理室主任田佳平所说,并非所有非金属材料都具备成本优势。简而言之,非金属材料也有等级之分,不同种类的非金属材料可以满足不同的功能要求,在具体成本上也存在差异。
在非金属材料中,碳纤维是公认的成本较高的轻量化材料。尽管目前有很多车型大量采用碳纤维,例如蔚来汽车在海外发布的一款EVE概念车,其碳纤维使用量便高达360公斤。但是大家一定知道,蔚来的这款车定位面向的是中高端人群,售价并不低。
当然,随着成本的优化,碳纤维也在逐渐由高端向中低端车型延伸,但至少从目前看来,碳纤维并非非金属材料中使用较多的材料类型。根据吉利汽车此前发布的相关报告显示,目前在汽车上应用最多的非金属材料是工程塑料和通用塑料,包括PP、AB、PC、PA、PBT、POM等,而随着更高性能塑料的工业化开发,长玻纤PP、生物基材料等功能性材料逐步增加在汽车上应用。
前面所提到的LFT,也即长纤维增强热塑性材料,便是其中值得一书的非金属材料之一。据了解,长纤维产品目前已被应用在仪表板、前端模块、蓄电池托架、天窗连接板、底护板、换挡器支架等方面。而在此基础上,胡仁其进一步指出,目前,PP(聚丙烯)长玻纤等材料是性价比较高的一种材料,原因是PP与长玻纤两者成本都相对较低,而通过两者的结合又能实现产品性能的提升,因此这一材料市场前景看好。
不过,他也补充说道,针对一些常规部件的使用,PP长玻纤的确具备较高性价比,但它并非适用于所有汽车零部件。吉利动力总成研究院袁爽在此前的一场演讲中同样指出,非金属材料有其优点,但也有不可避免的缺点,如由变形、刚度问题所带来的三漏问题。
袁爽认为,发动机各部件在选用非金属材料时要有明确的目的性,不可盲目跟从,汽车轻量化必须在保证汽车的强度和安全性能的前提下实施,对于确认的成果,必须应用非金属材料解决的问题,需要从成本下手,并提升可靠性,大面积推广。
总而言之,在国家严控汽车油耗及排放,轻质材料的采用不失为一种好的应对方案。而从以上专家的观点中也不难看出,在汽车轻量化过程中,最重要的或许并非车企采用的是何种材料,而是要恰到好处的应用这些材料,做到物尽其用。